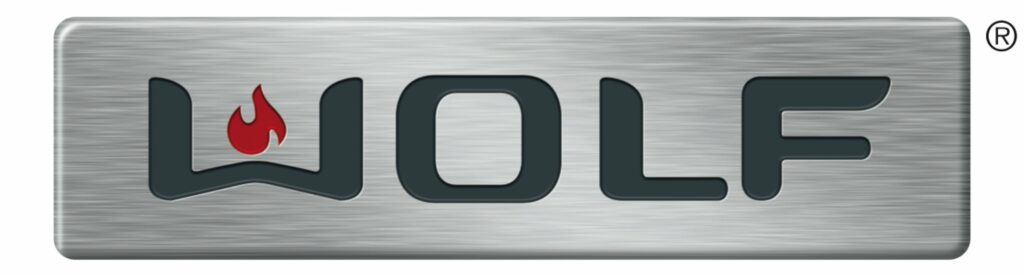
COMPANY PROFILE:
Launched in 1945, Sub-Zero Freezer Co. introduced the first system for preserving food at ultra-low temperatures. The company quickly established a reputation for quality and innovation. The third-generation, family-owned business, which operates as Sub-Zero Group Inc. based in Madison, Wisconsin, consists of three divisions – Sub-Zero refrigerators and freezers; Wolf Appliance cooking appliances; and Cove brand dishwashing equipment. The company operates a plant in Fitchburg, Wisconsin, and two Arizona facilities in Goodyear and Phoenix. Overall, the company has more than 500 employees.
SITUATION:
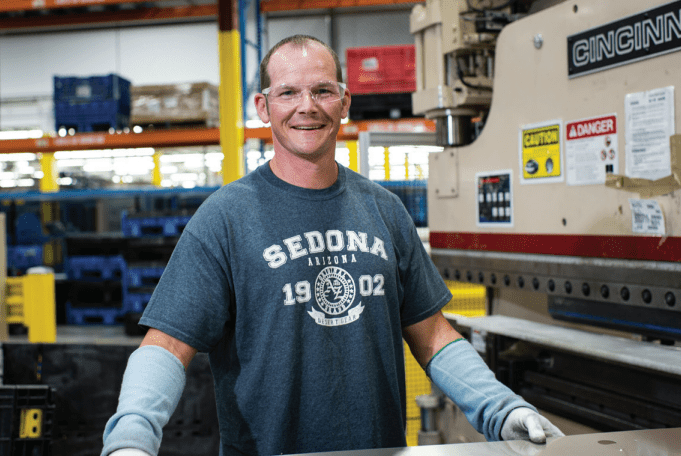
Wolf Appliance Co. sought to implement a Lean Manufacturing project to confirm to the company’s ownership and management that the Lean pathway can create measurable results and justify additional resources and support for future initiatives. The company needed outside assistance to implement this project due to a lack of internal resources and capabilities. The project focused on a 5-Axis laser cutting machine and the need to improve a bottleneck work center fed by seven supporting processes. Wolf management wanted the on-time efficiency of the laser increased by at least 20%. The laser is run 24 hours per day, six days per week.
SOLUTIONS:
Consultants from WMEP Manufacturing Solutions worked with Wolf Appliance project teams on Total Productive Maintenance training. Following the training, the project team collected Overall Equipment Effectiveness (OEE) data on its laser operations and used the data gathered to focus on major areas of lost time to direct and justify where improvements needed to be made. WMEP facilitators assisted the team with the implementation of the improvements.
RESULTS:
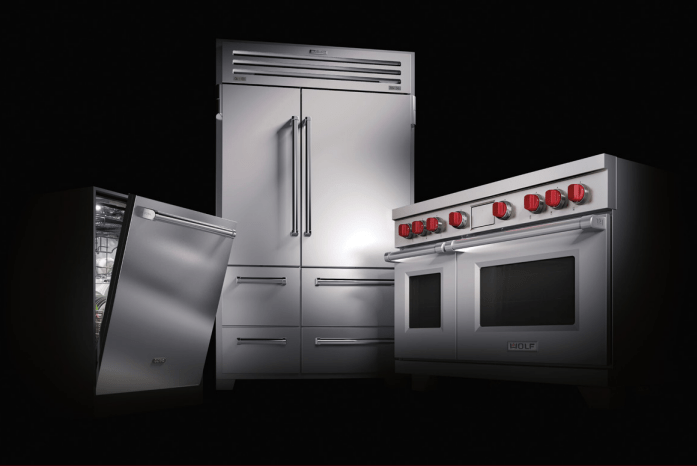
- A 36% increase in OEE per day, leading to 29.05 hours increased per week
- $1.91 savings per bezel ($24,830 per year)
- Laser on-time efficiency increased to 73% from about 50%
Sub-Zero has used WMEP for training and project facilitation for many years and still uses the TPM process.
Dave Burgette, Site Leader – Sub-Zero/Wolf Appliance